top of page
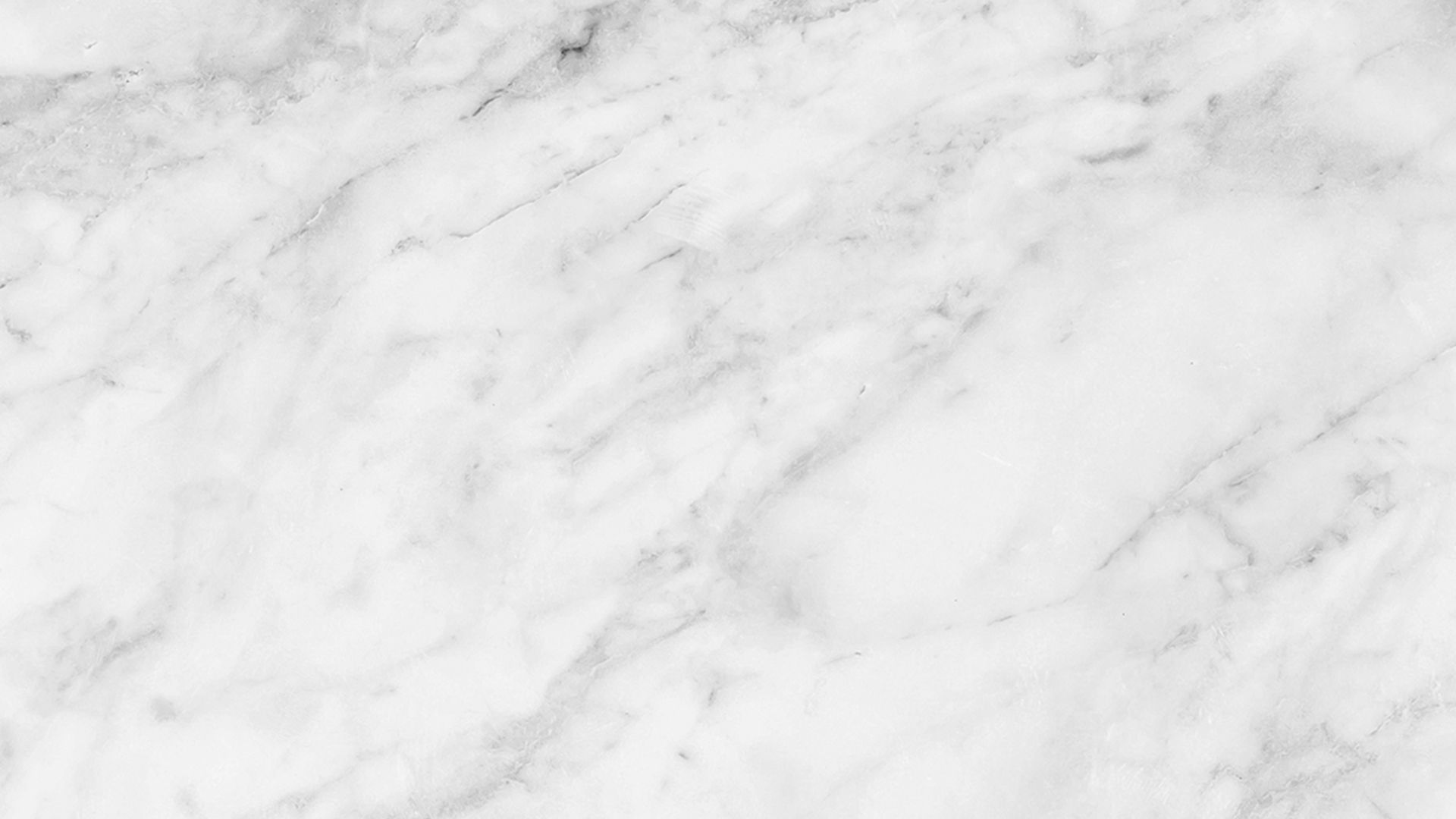
It takes a lot to build a custom board...

It all starts with a design idea...

Choosing wood
from my stock

This design will use 6 woods

Over to the tablesaw
to cut wood into strips

Strips are cut to length then...

laid out in the desired order

Pieces are glued and clamped...

and allowed to dry overnight
After several hours of drying time...

It's several passes through the planer to even everything out

Then the outside design is chosen and cut with a jig saw

Then several passes through the drum sander

Handles are chosen
Then the finish sanding begins...

I go through 4 different
grits on an orbital sander to get the desired finish

Then the boards are sprayed with water to raise the grain and prepare them for the final hand sanding with a very fine sandpaper

Then the boards are ready for a 30 minute bath in food grade mineral oil

Finally, 2 coats of bees wax are applied and hand rubbed to a soft luster
So after thinking about what I want to make, it goes....
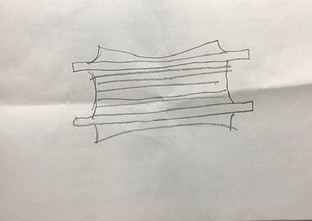
From this....
.jpg)
To this!!!
bottom of page